Thread-lockers: DIY or Pre-apply?
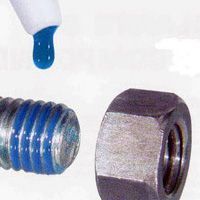
The Dawn of Thread-lockers
Soon after man invented the threaded fastener, we discovered the need to prevent those fasteners from coming loose.
Locking mechanisms are required when vibration or joint movement could cause loss of clamp load and joint failure. Today, thread locking mechanisms in some form are used in virtually every industry.
Thread lockers fall into three general categories:
- Free-running
- Prevailing torque
- Chemical reaction
Comparing Thread-lockers
This comparison will be focusing on the two most widely used, mechanical and chemical. More specifically, pre-applied (which could be either mechanical or chemical) vs. a liquid thread locking compound applied at time of installation.
The Industrial Fastener Institute (IFI) has developed standards for both mechanical and chemical types, IFI standards 124, 124, 524, and 525 cover thread-lockers for externally threaded fasteners, with standards 155, 160, 555, and 560 covering those with internal threads.
The main reason for using a thread-locker is to ensure quality control, avoiding joint failures, warranty claims, and potential liability issues. Engineers can select the best methods for a given application by understanding the capabilities and characteristics of the various types of thread locking mechanisms.
In a production environment, it may be advantageous to use a pre-applied thread-locker for several reasons.
Why Pre-Applied Thread-lockers?
Consistency: Pre-application of thread-lockers is performed in a carefully controlled process, ensuring that the thread-locker is in the correct location, and the correct amount, thereby keeping torque factors constant. Left to individual personnel, the amount and location of the thread-locker will tend to vary and could potentially be forgotten altogether.
Efficiency: Having thread-lockers pre-applied saves time and money, allowing line personnel to focus on assembling products rather than stopping to apply a liquid thread-locker to individual fasteners.
Mechanical vs Chemical Thread-lockers?
There are several factors to consider when choosing the best thread-locker for a specific application.
Chemical Thread-lockers
Chemical thread-lockers are available in multiple strengths, with the higher strength versions requiring heat to remove. These will provide lower installation torque, higher locking strength and breakaway torque but prevent any adjustability and are typically a one-time use.
Nylon Thread-lockers
Nylon thread-lockers will have a higher installation torque (due to the friction created between mating threads) lower breakaway torque, but their locking strength is less than that of a chemical adhesive. The nylon thread-locker however, is adjustable after installation and due to the memory characteristics of nylon, can be removed and reinstalled several times.
Pre-applied Thread-lockers
Pre-applied thread-lockers can be mechanical or chemical.
- Chemical in the form of micro-encapsulated beads within a resin. Installing the fastener breaks the beads, releasing the adhesive and setting off the reaction and curing process.The mechanical thread-locker of choice is nylon, available as a patch, pellet, or strip, and can be customized for more or less prevailing torque depending on the number of threads to which it is applied.
- Nylon is also the least expensive material, and because it is typically priced as a lot charge the price/ea. drops dramatically as quantity is increased, making it a very cost-effective process at production volume(s). This does need to be outsourced, as the parts must be heated to over 400º for the nylon to adhere to the threads.
As you may have gathered by now, there are many different types of thread-lockers available, as well as many reasons to utilize them on your fasteners.